Corporate Responsibility Report 2022-2023
Outcome 01 – Safe, healthy and quality working lifes for our people
Safety
We must be aware that we are working in a particularly challenging sector, where all the major safety risks come together. This makes us more vulnerable compared to other sectors, while society – rightly – expects from us zero tolerance when it comes to accidents. Our safety bar is therefore high: we do not want to accept major accidents anymore.

A strong safety culture is crucial to achieve ambitious safety results. Safety must be part of our DNA. Therefore, at the beginning of 2023, we started a very intense coaching exercise with support from the external firm dss+ (Dupont Sustainable Solutions) to achieve a change of culture in the field of safety.
The coaching focuses primarily on strict, uniform training and consistent application of our safety rituals (including safety conversations, safety quarters, risk analysis, ‘golden handshake’). A second essential element of SAFE Coaching is caring for each other. We need to take care of each other’s safety and dare to speak to each other about safety. These two essential elements of SAFE Coaching will help us to eliminate the grey zones – the unclear safety situations – and avoid serious accidents.
When we look at our safety dashboard, unfortunately, there is only one thing that really sticks, namely the serious accidents we have experienced in 2023. Reducing these major accidents is therefore our first priority. Fortunately, the number of these serious accidents is on the decline.
Our frequency figures (1.5 in 2022 and 1.7 in 2023) were not going in the right direction and hence we need to achieve a turnaround on each of the 3 pillars of our safety policy: People, Organization and Technique. To improve our health and safety results we focus on following topics:
- People – Leadership at the shop floor:
- The hierarchical line should be at least 2 hours a day present on the shop floor, the Management Committee minimum 2 hours a week.
- We want to increase safety by performing shop floor audits. The overall quality of the safety talks should be monitored and increased.
- During the Raise the Bar visits, it is asked to prepare a tour on the shop floor in which a maximum of cases is presented regarding shop floor presence, the human aspect and fatality prevention.
- We strengthen the safety communication with the employees using physical safety quarters, given by the N+1. Each month, there is a thematic quarter based on a specific Fatality Prevention Standard.
- Organization – Raise the Bar:
- It is necessary to realize the Start Work Risk Analysis on the shop floor. Via the golden handshake, we ensure that the necessary information (work permit, TRA, etc.) is discussed before the work starts.
- The work instructions are further improved.
- After incidents, we must define measures based on the human factor analysis.
- We continue to give the Take Care Training to all our (new) employees, and we optimize the Leadership Training with a module on ‘subsidiarity’.
- The level of discipline is increased by checking the behavior through counting the good and bad practices.
- Technique – Fatality Prevention:
- We deploy a structured approach in the departments to meet and audit the Fatality Prevention Standards requirements.
- The machine non-conformities and fatal risks will be identified, the so called ‘Black Points’.
- A Safety Alert can be announced in (a part of) a department for a period of 3 months. It is triggered by a serious occurrence or a worrying evolution of safety KPI’s. The goal is to change safety culture (“Technique” and “People”) using a highly increased focus on safety.
- We will raise the safety level through the implementation of SAP-WCM as the tool for consignments.
Health and Safety Day
On April 28, 2022, a new edition of the ArcelorMittal Health & Safety Day took place. The theme was ‘passion for health and safety’. During this Health and Safety Day, we also reflected on our five major risks: gas hazards and confined spaces, lock-out, vehicles and traffic, working at height, cranes and lifting. We therefore asked all departments to make their own video around one of these five major risks and/or about health. At least 30 varied videos were sent in, an overwhelming success. To keep the main risks under constant attention, an annual safety calendar was distributed in which every two months we highlight a different safety risk every two months.
The focus during the 2023 Health & Safety Day was on the life-saving golden rules. Every accident is avoidable if we follow the life-saving golden rules strictly.
Safety Survey
In February 2023, we launched a safety survey within ArcelorMittal Belgium, to evaluate how our collaborators experience our Health & Safety culture. The survey was conducted in all sites of the ArcelorMittal Group worldwide. The processing of the results was done by the external company dss+ (Dupont Sustainable Solutions), which supports the ArcelorMittal Group as well as our cluster in the implementation of our health and safety Action Plan. The study revealed that most departments are positioned in the dependent stage on the Brady Curve.
Health
In addition to safety at work, we are also committed to the health of our employees, both mental health and physical health:
Mental health
We are aware that as an employer we also have an important contribution in the mental health of our employees. We have seen an increase in work-related stress reports over the past two years, through following channels:
- The consultations with the occupational physician
- The reports to the confidants
- The well-being survey conducted among all employees in 2021 and the SpeakUp+, the quarterly survey, organized among the exempts.
Caring for each other, caring for our employees is our first priority. That is why we launched concrete actions, in consultation with the occupational physician, HR, confidants and the psychosocial prevention advisor and management.
- The resilience barometer has been introduced into the performance and appreciation interviews for white-collars and exempts. Employees who rate their own resilience low are invited by colleagues from the People Development Team to understand what the causes are and to discuss concrete actions at the individual, team, or organization level. It is also important that supervisors discuss this with employees who rate their own resilience low.
- The training on resilience at work (voluntary for employees, mandatory for new managers) was reworked. There is now also a possibility to organize this at team level, so that causes can be identified within the team and solutions can be sought together.
- The occupational physician can also support, using the “Burnout Assessment Tool” (BAT). This is a questionnaire to make a risk assessment on burnout and, based on this, discuss concrete actions with the occupational physician.
- ArcelorMittal Belgium cooperates with the external organization “Pulso,” so that in case of work-related stress collaborators can appeal to the support of an external psychologist for 5 sessions, fully paid by the employer.
- Walking in nature has been proven to have a positive effect on our mental well-being. It helps us to rest, clear our heads and refuel energy, to “de-connect. That is why it was decided to open the Rostijne forest at the ArcelorMittal Gent premises for a walk during the lunch break.
- In accordance with the labor deal which aims to alert employers and employees to the risks of continuous availability, a collective bargaining agreement was also drawn up within our cluster that defines the right to deconnection. The core of the right to deconnect is that employees are not required to be connected. The deconnection policy (including a deconnection charter) within our cluster goes beyond that and includes:
- realistic scheduling of duties within the position
- the importance of extended vacation time
- proper mail and meeting rules and guidelines regarding the use of digital communication tools
- the importance of focus time and time for professional development
A communication campaign was launched, including posters with cartoons and practical tips. In addition, mandatory e-learning courses were organized for foremen, employees and exempts on effective communication and efficient meetings. A training course was also organized around the efficient use of digital communication tools such as Outlook and Teams with a focus on deconnection.
Physical health
Regarding physical health, we want to focus on clearing the backlog of medical examinations due to corona. We want to pay attention to health risks: chemical agents, maternity protection, screen ergonomics, noise. We also want to ensure that first aid qualifications are better distributed among employees.
Quality in the working environment
Well-being of the collaborators
There are many issues coming our way in the coming years, such as “war for talent”, sustainable employability, training… We need to find solutions in the context of working longer in a continuous environment, the search for bottleneck professions, the impact of climate change (including hotter summers) on our working conditions, a “nervous” labor market with a need for more flexibility, the need for a healthy work-life balance. This calls for tailor-made flexible solutions, supported by technology and addressing individual needs.
Personnel survey
We strive to create a warm and safe working environment where everyone feels comfortable and where our values are central: cooperation, openness, respect, and subsidiarity. To know the concerns and expectations of our employees, a survey was launched in October 2023, which goes by the name “SpeakUp+” or “Uw mening telt” or “Votre avis compte”. This is a recurrent survey, allowing the evolution of certain themes and the outcome of action plans to be monitored.
Diversity and inclusion
Various groups in society express a clear expectation to companies to fulfill their responsibility when it comes to welcoming diversity and ensuring an inclusive work environment:
- Employees expect action to ensure the well-being of all.
- Candidates ask about it in the application process.
- Clients and partners make it a requirement to start a collaboration.
- Governments audit us about it.
- Investors include it as investment criteria.
Diversity and Inclusion are important issues in our society, but also in our company. We want everyone to feel welcome, both colleagues with a lot of experience and young talent, both innovators and enforcers, both thinkers and doers.
The population of employees within our company should reflect the profiles in our society. This means:
- more women in manufacturing environments
- more men in departments where mainly women work
- different nationalities and cultures
- different qualifications, diplomas and backgrounds
- all ages
- workers with a migration background
- a wider range of skills and competences
- different orientations
- reintegration of workers with medical disabilities
- …
When you bring together ideas and talents of employees with different profiles, backgrounds, and experiences, you get a more balanced decision-making approach. Inclusion thus makes us more creative, flexible, and ultimately stronger.
Our values – openness, cooperation, and respect – fit perfectly with this. With the combination of our similarities and our differences, we create an environment where we can give the best of ourselves.
We stand for an equal opportunity policy where we value diversity and inclusion. We are pleased within our organization with the first steps we have taken in terms of diversity and inclusion, e.g., ergonomic infrastructure adjustments, the increase in the number of new colleagues with a migration background, surveys, the focus on diversity and inclusion in training. But we recognize that we can go even further.
On May 17, the world celebrates the International Day Against Homophobia and Transphobia. An important day to reflect on and show solidarity with the LGBTQI+ community. Diversity and inclusion are important pillars both within society and within ArcelorMittal Belgium. That is why rainbow flags were flying at our 4 sites.
March 8 is dedicated to International Women’s Day. ArcelorMittal Belgium likes to highlight that day, but deliberately chose to focus on more than just gender. That is why ArcelorMittal Belgium made it a Day of Diversity.
ArcelorMittal Belgium’s Management Committee also drew up a Diversity Charter underlining his/her commitment to an inclusive workplace for all. The signing of this charter is a crucial step towards creating a working environment in which every employee feels at home. It symbolizes the concrete actions our cluster is taking to improve diversity and inclusion.
We have also trained HR management in legislation regarding several topics such as social media use and how employees out their opinions on D&I matters, praying at the workplace, as well as how to avoid biases, humor on the shopfloor and so on.
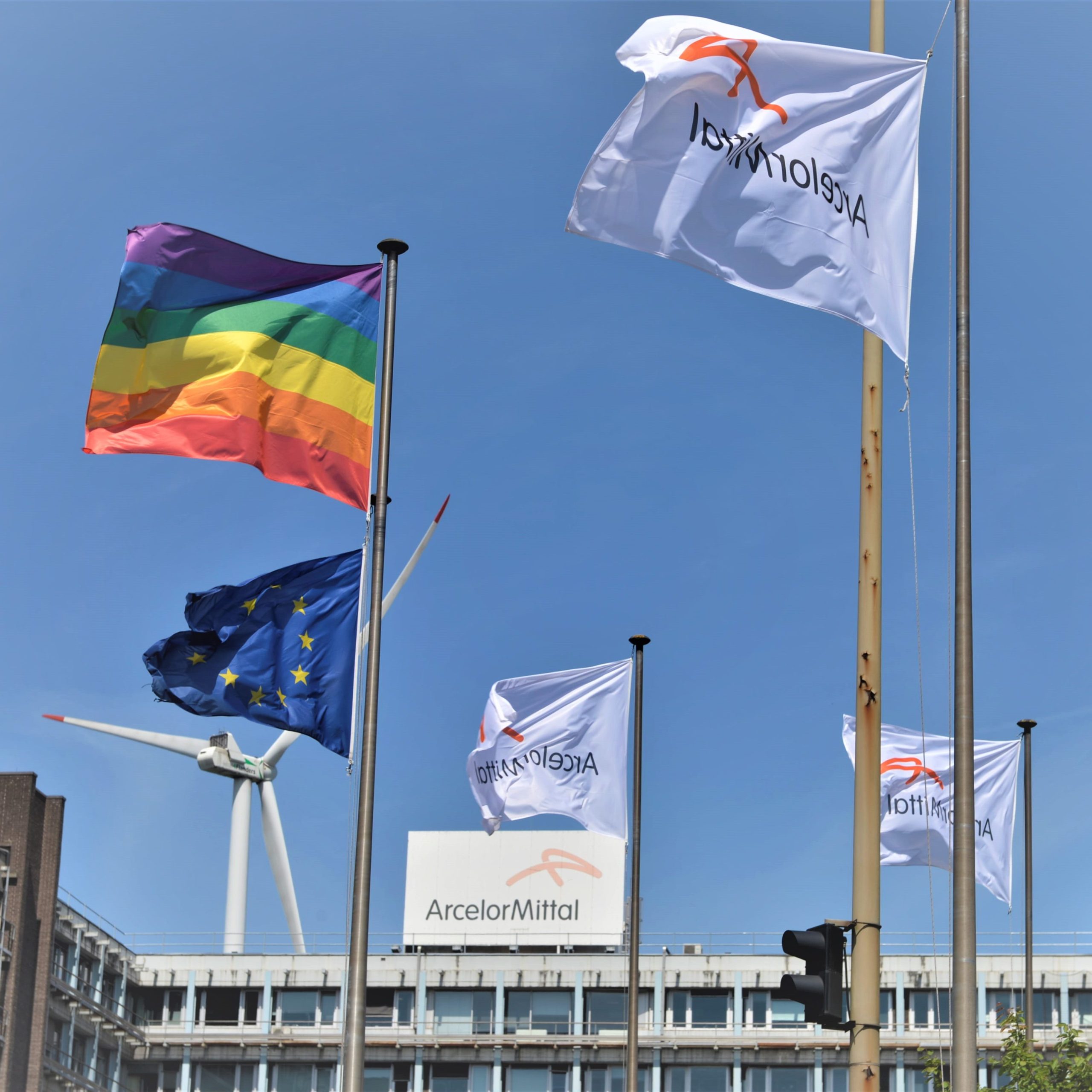
4 Commitments
After a difficult year of crisis and social unrest in 2021, several HR themes have been worked out in consultation with the social partners, linked to the 4 commitments (respect, occupancy problems and workload, working conditions, financial remuneration and conditions). These themes include time registration, growth function for work preparers, replacement pay for (reserve) foremen and zone pilots, evolution of remuneration for entry-level production workers and white-collar workers, evolution of maintenance functions for blue-collar workers, appreciation for on-the-job training.
Career development
Team reviews were introduced for all personnel categories. Since 2023, this was also the case for blue-collar workers to detect technical or managerial potential, and to engage in the further development of the individual employee. This made it easier to gain insight into gaps within the team and thus to be able to recruit in a more targeted way with a focus on missing competencies in the team.
Soft landing jobs
As from March 1, 2020, employees aged 58 or older employed at ArcelorMittal Gent, Genk and Geel can enter a soft-landing job. In concrete terms, this means that employees aged 58 and over can opt for a change of job and/or a change of shift regime (less stressful). Full-time employees can opt for 4/5th employment from the age of 60. A working group has also been launched in Liège to work out measures to keep older employees longer at work.
Career conversations 55+ were launched, where we first go through 3 pillars of sustainable career management in group sessions and for those who have individual questions provide an individual career conversation.
Mutual shift changing
In the joint working group CAO 104, initiatives are being worked out to make longer working more bearable for employees. In spring 2019, a pilot project was launched whereby employees employed in the full continuous shift system could change their first four nights with a colleague from the early shift and vice versa. In 2020, this project was further rolled out in the other departments. This project is now fully up and running and is gratefully used by a few tens of employees across the organization.
Hybrid working environment
It is now three years since COVID-19 required us to take various measures to protect our health. One of the measures was that many of our employees had to work compulsorily from home. Fortunately, this time is behind us, and we can once again physically work together in our offices. COVID-19 also taught us how to meet efficiently with new tools and collaborate in a more flexible way of working together. For this reason, we have adapted within ArcelorMittal Belgium our policy on homeworking to a maximum of 2 days of homeworking per week.
Digitalizing HR
Digitalization offers unprecedented opportunities, including for HR. A good example is the digitalization of absence requests and shift scheduling. IT developed two applications for this, the ‘ShiftPlanningTool’ and the ‘Group Calendar’.
At the end of 2020, all employees who did not already have this were allocated a professional e-mail address. General communications concerning safety, personnel matters, training… can thus easily reach everyone. Specific, local communication within the department can also be better supported this way. Moreover, access to e-mail gives all employees the opportunity to be in direct contact with the management and to disseminate essential information within a team.
Green mobility
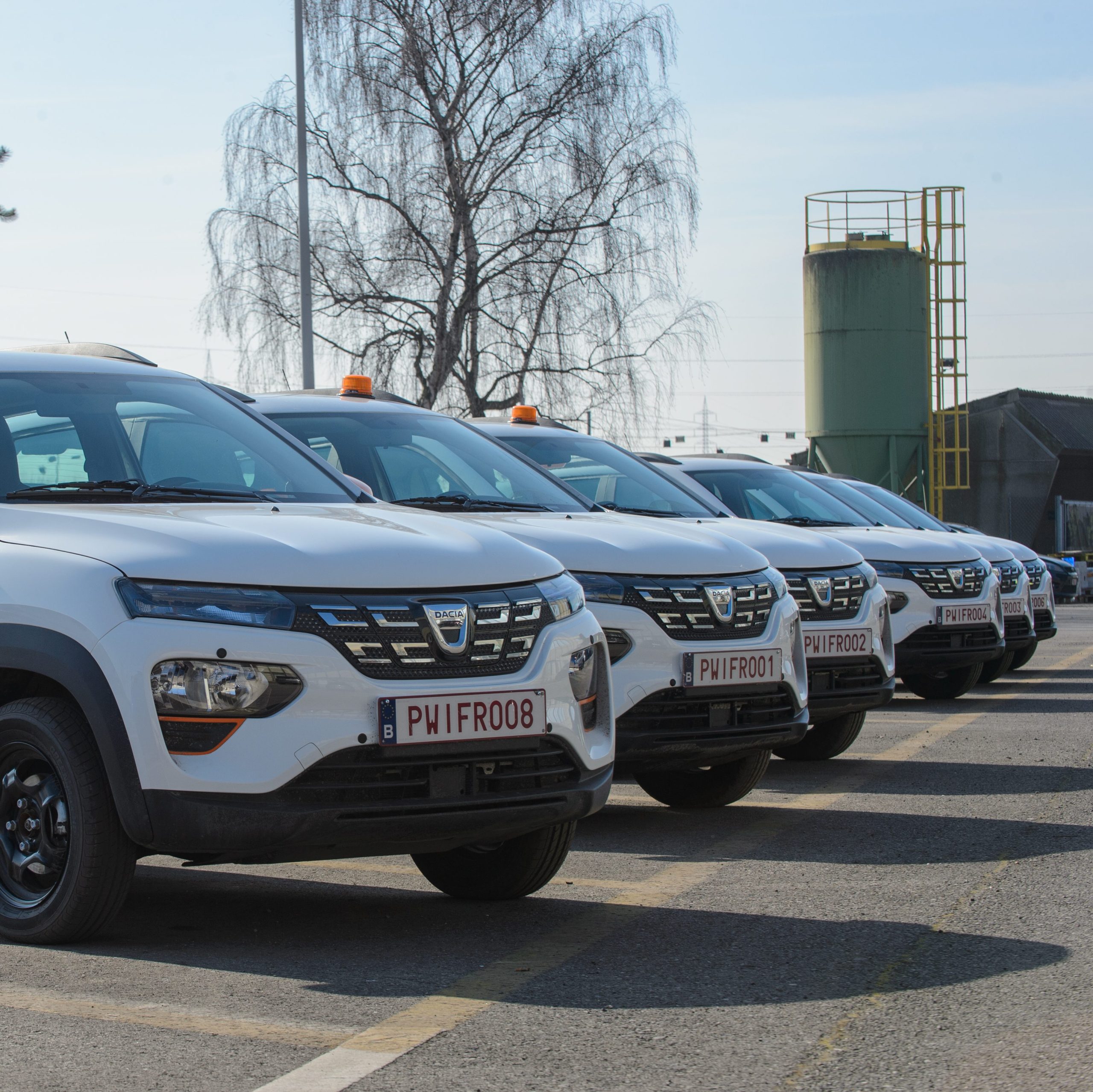
Our ambition is to ‘green’ our mobility by 20% a year. We promote sustainable commuting and note that our employees are increasingly choosing a sustainable option in terms of mobility. In ten years, the number of bicycle kilometers travelled daily by our colleagues towards our site has doubled. They are also increasingly opting for electric cars, for instance.
The car and bicycle leasing programs within ArcelorMittal Belgium were renewed in 2020. The key points of these leasing programs were:
- Lowering the maximum CO2 limit to 115 g
- Encouraging the choice of cars running on non-fossil fuel
- Facilitate charging infrastructure at our sites for ‘plug-in’ hybrid and electric cars.
- By the end of 2021, we will have evolved to 100 charging stations.
- Employee choice of contract with reduced mileage.
- Possibility of combining car and bicycle leasing
Since mid-2023, only electric cars can be leased.
Family Day
No fewer than 9,000 employees and their families registered for the second edition of our Family Day on June 25, 2022. The Family Day took place at the Walibi amusement park. It was a successful day filled with smiling faces and a strong group feeling that we will carry with us for a long time to come.
Decoration Happening
Every year, all employees of ArcelorMittal Belgium with a career of 25 years or more are treated to a festive day where atmosphere and togetherness are key.
60-year anniversary of ArcelorMittal Belgium
It was exactly 60 years ago, on July 10, 1962, that the NV “Sidérurgie Maritime,” Sidmar for short, was founded. Therefore, all internal employees of our cluster received an anniversary gift, a travel suitcase. Moreover, this trolley was a fine example of circularity and sustainability because it was made of recycled PET bottles.
Gent Jazz Festival and Festival of Flanders
ArcelorMittal Belgium participates as a sponsor in two Gent music festivals – Gent Jazz and Gent Festival van Vlaanderen – and as part of this, offers some 500 employees the chance to enjoy this event.
Review of internal communication
Communication around different topics and in different directions is very important in our organization. However, we note that some information is not known sufficiently or is known too late and, in the opposite direction, information from the shop floor does not reach the hierarchy. This was also expressed in the survey on the 4 commitments. Various initiatives have already been launched in recent months: initiatives to improve communication via information screens, intranet, newsletter, and other channels. Because the communication channels are constantly evolving, we decided to call on an external communications agency (Billie Bonkers) to find out what causes the insufficient flow of information and what we could do to change.
World Class Manufacturing
World Class Manufacturing (WCM) is the driving force behind continuous improvement. WCM is a solid approach and a strong framework to continuously improve and secure our efficiency. We need to focus on long-term goals and consistently follow our chosen ambition in this, from bronze to silver to gold.
In 2022 and 2023, three departments achieved the WCM ‘silver’ award: the cold rolling mill (pickling lines and tandems), the blast furnaces & sinter plants, and the Decosteel organic coating lines. Congratulations to everyone who contributed to this!
The WCM ‘silver’ award is symbolically nice as an appreciation for the efforts made, but it is more than a symbol. We note that departments with a solid WCM structure, such as the coking plant and general services, also make great progress in terms of safety results, organization of preventive maintenance and operational reliability. So WCM does lead to results and improves our business performance.
On October 3, 2023, the first WCM day took place within the ArcelorMittal Belgium cluster.
The objective was to highlight WCM projects and results and share knowledge with each other. After the official opening by management, several WCM initiatives were presented on the shop floor.
Training
Our employees are our greatest asset. That is why we are strongly committed to career development, offering the necessary training so that our employees can further develop their skills. Employees are also encouraged to take control of their careers themselves and think about their future where we offer numerous opportunities for those who want to progress. In 2022, ArcelorMittal Belgium spent 6.02% of the total wage bill on training and education. For 2023, this figure was 5.88%.
One of the biggest challenges we face is difficulty in hiring technical personnel. This challenge commits us to change hiring demands and adjust our training approach. The key points of the new training program for mechanics and electricians:
- Basic knowledge
- Practical approach
- Tailored to local needs
- Mandatory
- Following courses for continued growth
- Leadership
- Technical expertise
Further key points in training are:
- Start-up training of 1 week for all new collaborators
- Retraining program for production personnel to mechanics
- Training of SAP: safety and preventive maintenance
- Take Care training course with a strong focus on practice!
- Training of social skills
- Leadership training (360° assessment before and after)
- In 2024 additional training for leaders concerning inclusion, integrity and connection will be organized
- Digitalization of training (e.g., crane simulator, e-learning, etc.).
Cybersecurity awareness program
As part of our commitment to strengthen ArcelorMittal’s cybersecurity, we launched the ‘Europe-Cybersecurity Awareness 2023’ training on June 15. This training is mandatory for white-collar and exempts and is repeated quarterly.
Learning Week
Every year in June, a new edition of the ‘Learning Week’ takes place. During this ‘Learning Week’ we pay extra attention to learning and training. In 2022, the overall theme was ‘Boosting our Sustainability’. In 2023, the overall theme was ‘Be Consciously Curious’. Initiatives were taken in the field of health and safety, sustainability, teamwork, and innovation.
Training event
On June 16, 2023, a safety and training event was organized. The event took place at the Verbeke Foundation for all colleagues who in recent years had followed a maintenance training, had successfully passed the promotional tests in electricity or mechanics, successfully passed the promotion tests electricity or mechanics, completed the siderurgy course or for those who participated in a WCM pillar 8 case.