Corporate Responsibility Report 2022-2023
Outcome 04 – The efficient use of natural resources and high recycling rates
Our environmental care
We have an environmental management system in place since 2001 that meets the requirements of the international standard ISO 14001. The environmental management system obliges us to take a structured approach to our environmental care, starting with the identification of the important environmental aspects to which we must pay attention. Our environmental management system is audited each year by an external independent organization that assesses whether we continue to meet all standard requirements and whether we continue to improve on our environmental management. The ISO 14001 certificate provides a guarantee to all external stakeholders, such as residents, surrounding companies, authorities, suppliers, and customers, that ‘sustainable development’ is not a hollow phrase for us.
Our energy care
We have an energy management system in place since 2017 that meets the requirements of the international standard ISO 50001. The energy management system obliges us to take a structured approach to our energy care. Our energy management system is audited each year by an external independent organization that assesses whether we continue to meet all standard requirements and whether we continue to improve on our energy management. The ISO 50001 certificate provides a guarantee to all external stakeholders, such as residents, surrounding companies, authorities, suppliers, and customers, that ‘energy efficiency’ is not a hollow phrase for us.
By-products, residues, and waste materials
We strive towards avoiding the generation of waste as much as possible and converting all substances that are produced and used during the production of steel into products that can serve as raw materials in other industries or that have a useful application.
By-products
By-products are materials that are either reused as a raw material or used as a synthetic end product as an alternative to e.g., natural stone.
Residues
Residues are mainly residues containing ferrous oxide and carbon which are inevitably formed during our production process, and which are separated from a gas or water flow in our dust separator or water treatment plants.
Waste materials
Waste materials are materials that cannot easily be re-used. We collect them selectively. Most waste materials are recovered by accredited processors. Only a relatively small quantity is dumped or incinerated. Some examples:
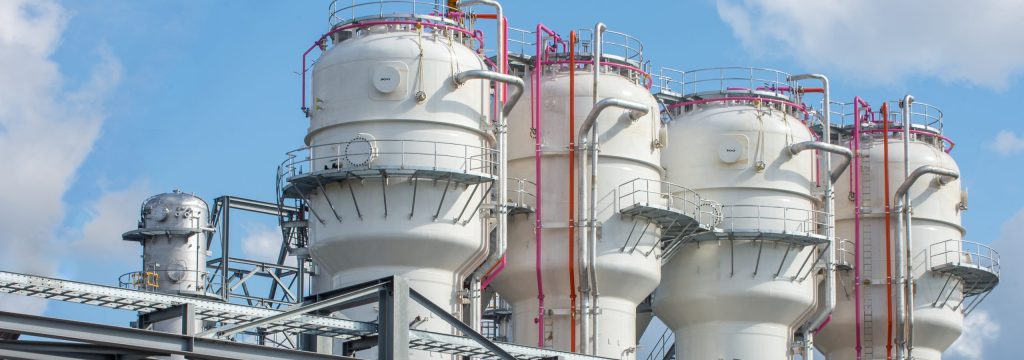
Steelanol: blast furnace gas becomes ethanol
On June 14, 2023, ArcelorMittal and LanzaTech Global Inc. announced the successful commencement of production from ArcelorMittal’s commercial flagship carbon capture and utilisation (‘CCU’) facility in Ghent, Belgium. The €200 million ‘Steelanol’ facility is a first of its kind for the European steel industry, deploying technology developed by leading carbon utilization company LanzaTech.
Mid-June 2023 saw the first step toward full operation of a commercial scale facility that will capture carbon-rich waste gases from steelmaking and biologically convert them into ethanol through LanzaTech’s bio-based process. Unlike traditional fermentation, the process ferments gases instead of sugars and uses a biocatalyst instead of yeast. The facility was inaugurated in December 2022, with cold commissioning taking place thereafter. The biocatalyst has now been introduced into the facility (a process called inoculation) to begin growth and verify production of new molecules.
Read more
In May 2023, the first gases from the steel mill’s blast furnace were safely introduced to LanzaTech’s biocatalyst. After a successful inoculation, initial samples that contained ethanol were produced, demonstrating that the carbon in the gases is being converted into new chemical products. Commercial-scale ethanol production from the bioreactors will follow, with expected ramp up of production the next months. This ethanol can then be used as a building block to produce a variety of products, including sustainable transport fuels, packaging materials, apparel, and even cosmetic fragrances, hence helping to advance the decarbonization efforts of the global chemical sector. The ethanol will be jointly marketed by ArcelorMittal and LanzaTech under the Carbalyst® brand name.
The Steelanol plant has the annual capacity to produce 80 million litres of advanced ethanol, around half of the total current demand in Belgium. It expects to reduce carbon emissions from the Ghent plant by 125,000 tonnes annually, thereby advancing the EU’s 2030 Climate Target Plan to reduce greenhouse gas emissions by 55% by the end of the decade. Project partners include Primetals Technologies and E4tech with support from CINEA, the European Climate, Infrastructure and Environment Executive Agency.
The product samples from the facility mark an important step toward the circular use of carbon and the end of single-use carbon, whereby gases are no longer regarded as waste but as raw materials. In addition, the recycling of carbon means Steelanol’s process of Carbalyst® ethanol production does not compete in any way with food crops, as is the case for traditional methods of ethanol production.
The LanzaTech process implemented at this site is fully flexible: not only can it use industrial gases from today’s steel production methods but also it can adapt as industry transitions to future steel production technologies with increased green hydrogen input. This versatility enables the carbon recycling application to evolve with available residue, waste streams, and green H2. LanzaTech’s process is already employed by three operational commercial facilities, and LanzaTech anticipates the launch of two additional commercial facilities, in Asia, before the end of the year.
Funding for the commercial Steelanol facility was obtained from various sources, including the Flemish government, the Belgian federal government and the European Union’s Horizon 2020 research and innovation program under grant agreement No 656437. Part of the funding was also secured with a loan from the European Investment Bank.
In April 2021, ArcelorMittal Belgium launched a new project “SMART: Steelmaking with Alternative Reductants”. The LIFE SMART project is an innovative technique to reduce emissions by recycling end-of-life plastics and other waste. In the steelmaking process, so-called ‘reductants’ are needed to transform iron ore into hot metal. The LIFE SMART project allows us to replace fossil carbon-containing reductants such as coal with circular waste-based reductants. To this end, Vanheede Environment Group, an integrated environmental company located in Belgium, will supply ArcelorMittal with SRF (solid recovered fuel) AlterCoal pellets. These pellets are a mixture of organic waste, household waste and plastic with a high energy value. These AlterCoal pellets will be transformed into metallurgical coke and into pulverized coal. Both take on the role of reductant and energy source in the blast furnace. By reducing the use of fossil carbon, we will be able to reduce our CO2 emissions and provide a solution for particularly difficult waste streams, such as plastics. The SMART project is yet another step forward in our ambition to become the sustainable steel plant of the future, the cornerstone of a circular economy.
Beginning of 2023, North Sea Port, ArcelorMittal Belgium and all the port companies have committed themselves to a climate-neutral port by 2050. This will be achieved by reducing CO2 emissions and further developing the circular economy. To this end, the North-C Circular industrial estate is being developed in Ghent.
The development of the North-C Circular industrial estate is a joint initiative by North Sea Port and ArcelorMittal Belgium. Together, they will develop an industrial estate on the right bank of the Ghent-Terneuzen Canal in Ghent. The site lies between Rodenhuizedok, the port ring road R4 and the ArcelorMittal Belgium site. It is part of the port area that is designated for companies based in the seaport and along the waterways. The intention is to prepare this 150-hectare site for construction, install basic infrastructure like utilities, provide access by road, rail and water and move in companies geared towards circular activities.
Read more
A brownfield covenant is being drawn up for the entire site between North Sea Port, ArcelorMittal Belgium and the Flemish government. On 40 hectares of this site there are historic dredging sludge depots that are impeding the immediate development of the site. The covenant will enable this underutilised land to be transformed into an industrial estate in a comprehensive and structured manner and its use extended. The accompanying forest compensation will be conducted as much as possible in the vicinity.
When work on the industrial estate is completed, it will be ready to accommodate economic activities focused on reducing CO2 emissions, the energy transition from fossil to renewable raw materials, the circular economy and partnerships with companies in the surrounding area.